Denny330
Well-Known Member
I have been designing this in my head and on paper for over six months and finally decided to take the plunge and build it. This is an ongoing project so the updates will probably be slow coming, but I hope to have everything fully operational by the AHA Big Brew Day on May 5 so my Homebrew Club will have a place to brew.
First a little background. I was an electrician in the Navy and currently operate a commercial nuclear power plant, so I know about wiring and diagrams and overdesigning everything, but I don't remember too much from the NEC and I stopped paying attention to the NEC in 1997. If anyone sees anything dangerous or silly that I am doing, please for the love of all things holy tell me. Everyone knows how easy it is to overlook something after you have looked at it for months. I have a visio drawing of my wiring diagram, but I'll figure out how to post it up soon.
I have a separate thread for the stand if anyone is interested in that: Beer Robot Stand
The Beer Robot is an eHERMS design, 5500w element in the BK, 4500w element in the HLT, two chugger pump system, controlling 4 valves, all using the BCS-462 from Embedded Control Concepts. I had planned on using solenoid operated diaphragm valves until yesterday when I found others using these motor operated ball valves. So now I am going to have a 12v component of my control box. (Back to the design drawing board!
)
Speaking of control boxes, mine came in that wonderful SeaFoam green color that I promised would never be in my home (anyone who has been on a submarine can attest to the hatred). So I gave it the Bobby_M treatment.
(in process)
After the Bobby_M treatment:
I still have holes to cut so it will get another polishing at the end.
I will post more pictures as the build continues.
First a little background. I was an electrician in the Navy and currently operate a commercial nuclear power plant, so I know about wiring and diagrams and overdesigning everything, but I don't remember too much from the NEC and I stopped paying attention to the NEC in 1997. If anyone sees anything dangerous or silly that I am doing, please for the love of all things holy tell me. Everyone knows how easy it is to overlook something after you have looked at it for months. I have a visio drawing of my wiring diagram, but I'll figure out how to post it up soon.
I have a separate thread for the stand if anyone is interested in that: Beer Robot Stand
The Beer Robot is an eHERMS design, 5500w element in the BK, 4500w element in the HLT, two chugger pump system, controlling 4 valves, all using the BCS-462 from Embedded Control Concepts. I had planned on using solenoid operated diaphragm valves until yesterday when I found others using these motor operated ball valves. So now I am going to have a 12v component of my control box. (Back to the design drawing board!

Speaking of control boxes, mine came in that wonderful SeaFoam green color that I promised would never be in my home (anyone who has been on a submarine can attest to the hatred). So I gave it the Bobby_M treatment.
(in process)
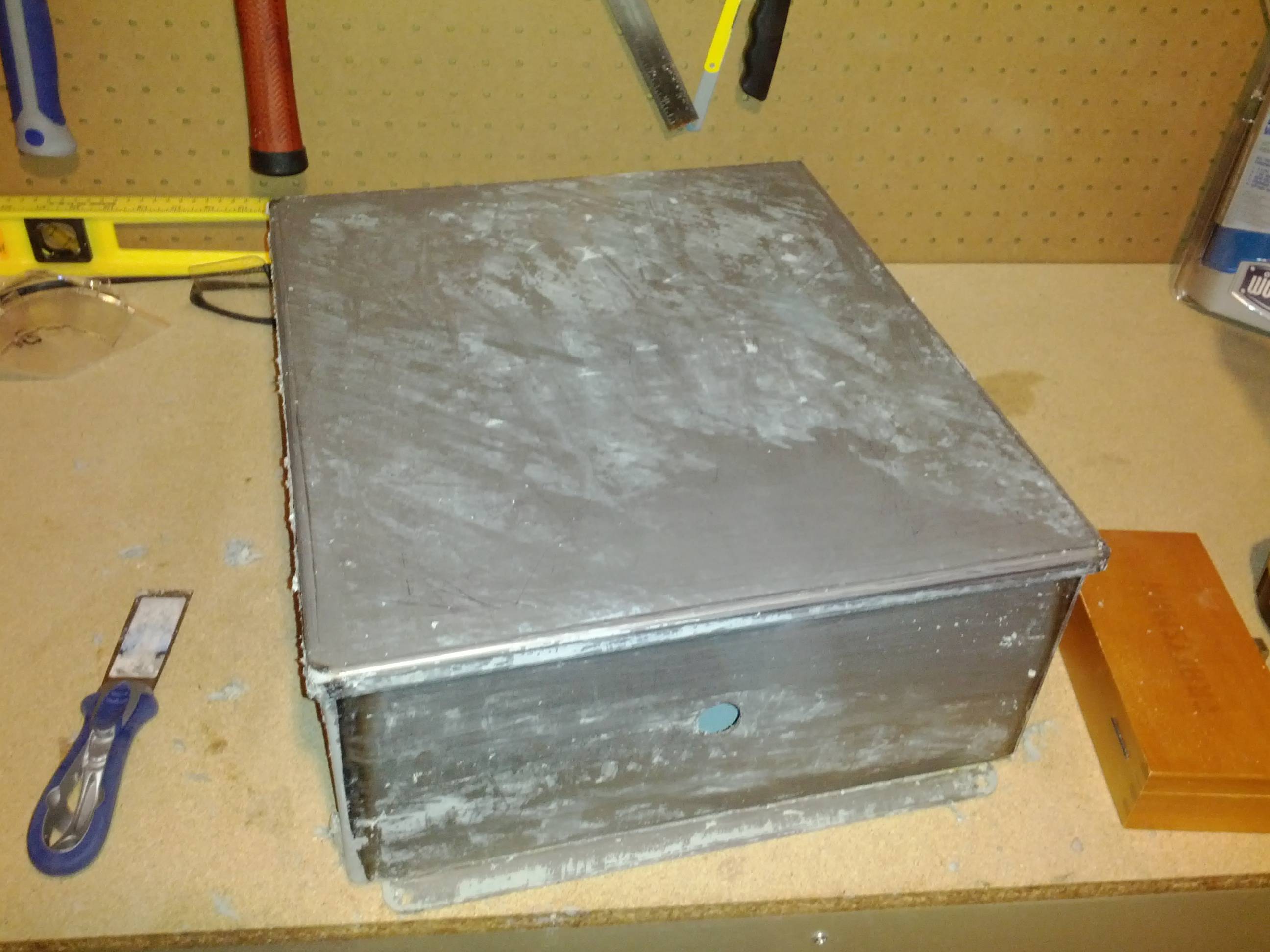
After the Bobby_M treatment:
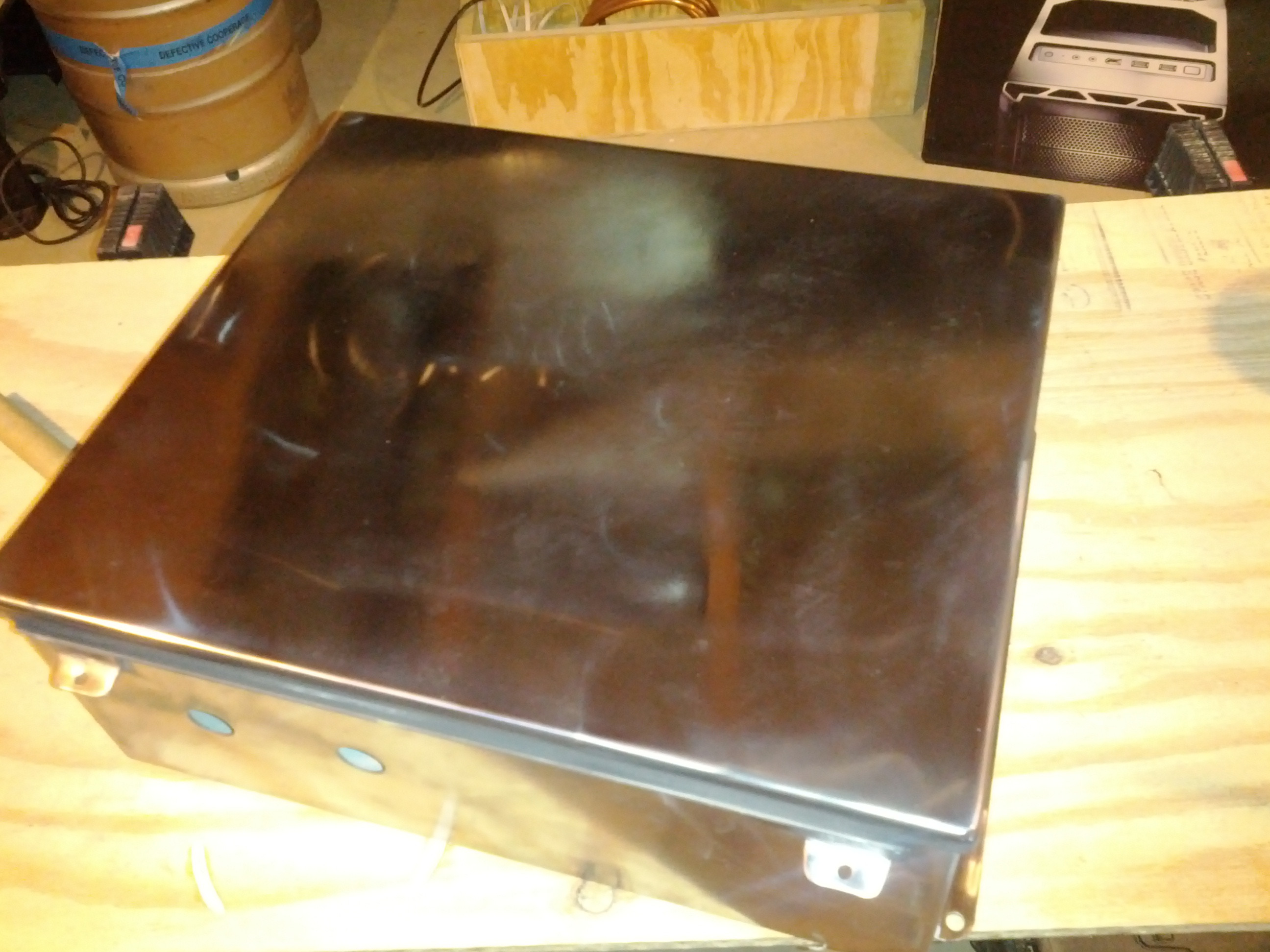
I still have holes to cut so it will get another polishing at the end.
I will post more pictures as the build continues.