After finishing up my garage I decided it was time to start my keezer project with my father-in-law. I've been reading and studying for quite a while and felt it was time to dive in head first myself.
I started by buying the chest freezer a couple months ago. I went with a new Igloo 10.0 cubic foot FRF1049 from Best Buy and paid $250 for it. The pic on the website isn't accurate at all to the actual size, it is roughly 43"x24"x34". http://www.bestbuy.com/site/igloo-10-0-cu-ft-chest-freezer-white/1542583.p?id=1219054918686
The interior dimensions will fit 6 corny kegs, so I decided to make a 5 tap keezer with my 10lb CO2 tank hosted inside. The hump can hold some spare beers, or I have a 2.5g and a 3g corny also I could swap into one of the lines.
I decided to make it out of birch after checking out the wood selection at my local Lowes. The pattern of the wood was just really great, and I can't stand the look of oak, it just reminds me too much of the furniture in my parents house growing up in the 1980's. Little did I realize that (apparently) birch is notoriously difficult to stain evenly. That is a problem for another day though and I am definitely doing my homework via youtube and online blogs.
Here is the start of the base well under construction already. We used some nice scrap 3/4" plywood for the base, supported by 2x4s and secured with counter-sunk screws. We used threaded carriage bolts to hold the casters. We also accidentally mounted the locking casters a bit too close to edge, so when locked they caught a bit on the framing. Nothing a chisel couldn't carve out though. >_>
Here's a shot of the bottom. You'll notice that some of the 2x4s are thinner than 2x4s...We were originally going to line the pine supports up flush directly with the bottom, then quickly realized it would have more strength if we were able to screw them directly into the 2x4 base supporting the whole structure. A quick couple trips through the table saw and we're ready to do that.
3" casters supporting 250lb each, so we're well within the 500-600lbs this should weigh when complete.
Here's a shot of the front with the finished birch plywood attached. Yes, we used screws to secure everything tightly. I've seen a lot of builds on here using straight glue, but we don't have the patience for it since the screws will be covered up by the veneer that boxes everything in anyway. These pieces were purchased in the size you see them, somehow we got really lucky and the two front panels are a perfect match from the same sheet and the grain lines up perfectly, which we think is very cool.
Here's a shot of the side. The birch plywood was just a bit shorter than the box length we needed so we used some scrap on the end, which will all be covered up by the veneer.
Here's a shot of the interior. You can see we backed it all with pine, and we reinforced all the joints with some steel bracketing for extra support (making sure our screws were the right length and didn't punch through the front of course
). We also drilled a couple big holes out in the bottom to allow for extra airflow just for kicks, figured it couldn't hurt and you'd never see it.
Here's the first piece of veneer we glued on (sorry, I'm sure there is a better/more appropriate word for these pieces but I can't think of one right now). This is on the left side of the freezer, and you can see it covers the screws up nicely. Since the 3" casters keep this well off the ground, we decided to let the veneer overhang the bottom a bit to help hide the wheels. We used Gorilla wood glue.
This is an inside shot opposite the one above. We don't have enough clamps to do a lot of the gluing all at the same time, so we counter sunk some very precisely measured screws and screwed into the piece being glued from the inside, but obviously without penetrating the veneer. For what it is worth, this worked extremely well.
Here's as far as we made it after our 2nd day of work. You can see the veneer on the right is thinner than the one on the left. The front panel veneer will sit directly on top of this, thus extending it by another ~3/4" so they should be exactly the same thickness when done, but with a seam obviously. Neither one of us wanted to go through the pain of mitering the edges together on the table saw, we just didn't think we'd be able to get it to look good at all, so we decided to go with a seam on the sides. We'll finish this veneer up with the bottom middle piece to complete the square next weekend.
That wraps it up until next weekend. We're hoping to get all of the veneer on and glued, and then we can get the freezer in the box and start to work on the top. I'll continue to post updates as we progress on the build!
~Cyn
I started by buying the chest freezer a couple months ago. I went with a new Igloo 10.0 cubic foot FRF1049 from Best Buy and paid $250 for it. The pic on the website isn't accurate at all to the actual size, it is roughly 43"x24"x34". http://www.bestbuy.com/site/igloo-10-0-cu-ft-chest-freezer-white/1542583.p?id=1219054918686
The interior dimensions will fit 6 corny kegs, so I decided to make a 5 tap keezer with my 10lb CO2 tank hosted inside. The hump can hold some spare beers, or I have a 2.5g and a 3g corny also I could swap into one of the lines.
I decided to make it out of birch after checking out the wood selection at my local Lowes. The pattern of the wood was just really great, and I can't stand the look of oak, it just reminds me too much of the furniture in my parents house growing up in the 1980's. Little did I realize that (apparently) birch is notoriously difficult to stain evenly. That is a problem for another day though and I am definitely doing my homework via youtube and online blogs.
Here is the start of the base well under construction already. We used some nice scrap 3/4" plywood for the base, supported by 2x4s and secured with counter-sunk screws. We used threaded carriage bolts to hold the casters. We also accidentally mounted the locking casters a bit too close to edge, so when locked they caught a bit on the framing. Nothing a chisel couldn't carve out though. >_>


Here's a shot of the bottom. You'll notice that some of the 2x4s are thinner than 2x4s...We were originally going to line the pine supports up flush directly with the bottom, then quickly realized it would have more strength if we were able to screw them directly into the 2x4 base supporting the whole structure. A quick couple trips through the table saw and we're ready to do that.
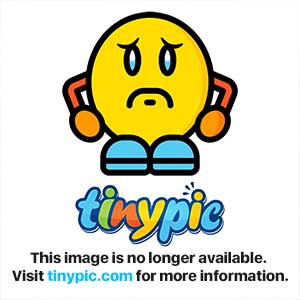
Here's a shot of the front with the finished birch plywood attached. Yes, we used screws to secure everything tightly. I've seen a lot of builds on here using straight glue, but we don't have the patience for it since the screws will be covered up by the veneer that boxes everything in anyway. These pieces were purchased in the size you see them, somehow we got really lucky and the two front panels are a perfect match from the same sheet and the grain lines up perfectly, which we think is very cool.
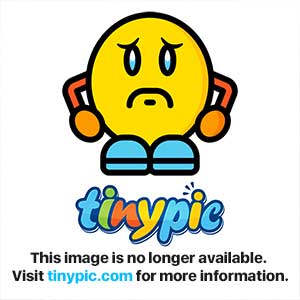
Here's a shot of the side. The birch plywood was just a bit shorter than the box length we needed so we used some scrap on the end, which will all be covered up by the veneer.

Here's a shot of the interior. You can see we backed it all with pine, and we reinforced all the joints with some steel bracketing for extra support (making sure our screws were the right length and didn't punch through the front of course
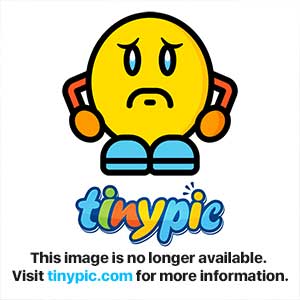
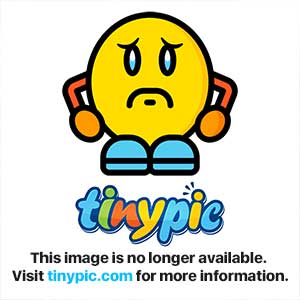
Here's the first piece of veneer we glued on (sorry, I'm sure there is a better/more appropriate word for these pieces but I can't think of one right now). This is on the left side of the freezer, and you can see it covers the screws up nicely. Since the 3" casters keep this well off the ground, we decided to let the veneer overhang the bottom a bit to help hide the wheels. We used Gorilla wood glue.

This is an inside shot opposite the one above. We don't have enough clamps to do a lot of the gluing all at the same time, so we counter sunk some very precisely measured screws and screwed into the piece being glued from the inside, but obviously without penetrating the veneer. For what it is worth, this worked extremely well.


Here's as far as we made it after our 2nd day of work. You can see the veneer on the right is thinner than the one on the left. The front panel veneer will sit directly on top of this, thus extending it by another ~3/4" so they should be exactly the same thickness when done, but with a seam obviously. Neither one of us wanted to go through the pain of mitering the edges together on the table saw, we just didn't think we'd be able to get it to look good at all, so we decided to go with a seam on the sides. We'll finish this veneer up with the bottom middle piece to complete the square next weekend.

That wraps it up until next weekend. We're hoping to get all of the veneer on and glued, and then we can get the freezer in the box and start to work on the top. I'll continue to post updates as we progress on the build!
~Cyn