Drilled some holes in the HLT today. One for the water outlet (bottom) and two for the heat exchanging coil.
Had to create som custom seals and here you can see the procedure to do that. The black mat is some woven thing that my plumber said would be the best since I will be working with stuff that is intended to drink and that can stand the heat.
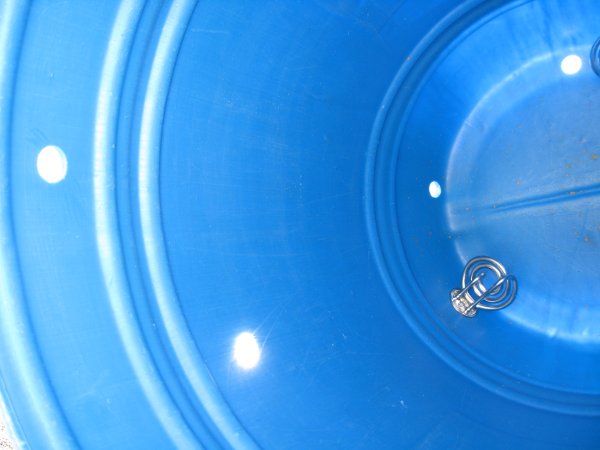
Had to create som custom seals and here you can see the procedure to do that. The black mat is some woven thing that my plumber said would be the best since I will be working with stuff that is intended to drink and that can stand the heat.
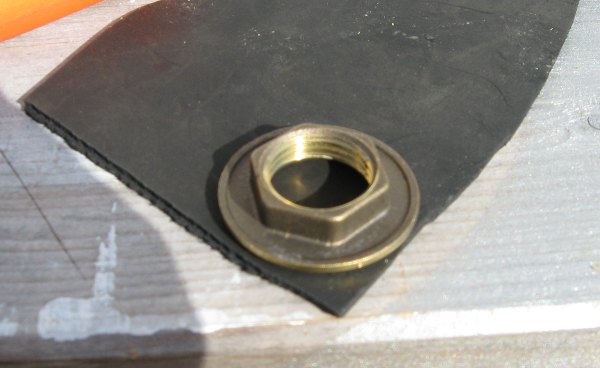
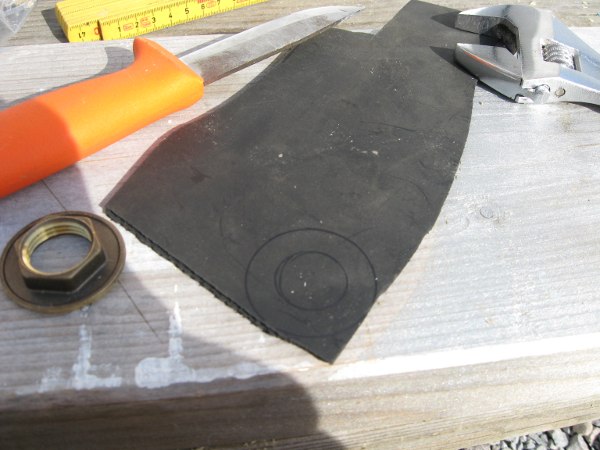