Hey all,
Been planning my single tier brewing system and I will have 2 march pumps (Both 110 volts). So I will be building a switch controller with an emergency stop (just in case). I am not super experienced with wiring, I understand the components and such but just haven't had the chance to actually do it.
So, please look at my diagram and see if I have made some mistakes and help me correct them if so. OR any advice to improve its functionality.
A list of the elements I will use:
A junction box similar to this
2 way NO switches
Emergency Stop
LED Light 'ON' indicators
Female Receptacle
Male Receptacle
AWG #14
All needed connectors/equipment
To give an idea of what I am doing with my brewing system. This will utilize 2 - 18" propane burners with two march pumps controlled by the switching module. I will also have all SS Brewing Technology (HLT/MT/BK). And a plate chiller which is not in these designs.
Any suggestions welcome.
Thank you!
Been planning my single tier brewing system and I will have 2 march pumps (Both 110 volts). So I will be building a switch controller with an emergency stop (just in case). I am not super experienced with wiring, I understand the components and such but just haven't had the chance to actually do it.
So, please look at my diagram and see if I have made some mistakes and help me correct them if so. OR any advice to improve its functionality.
A list of the elements I will use:
A junction box similar to this
2 way NO switches
Emergency Stop
LED Light 'ON' indicators
Female Receptacle
Male Receptacle
AWG #14
All needed connectors/equipment
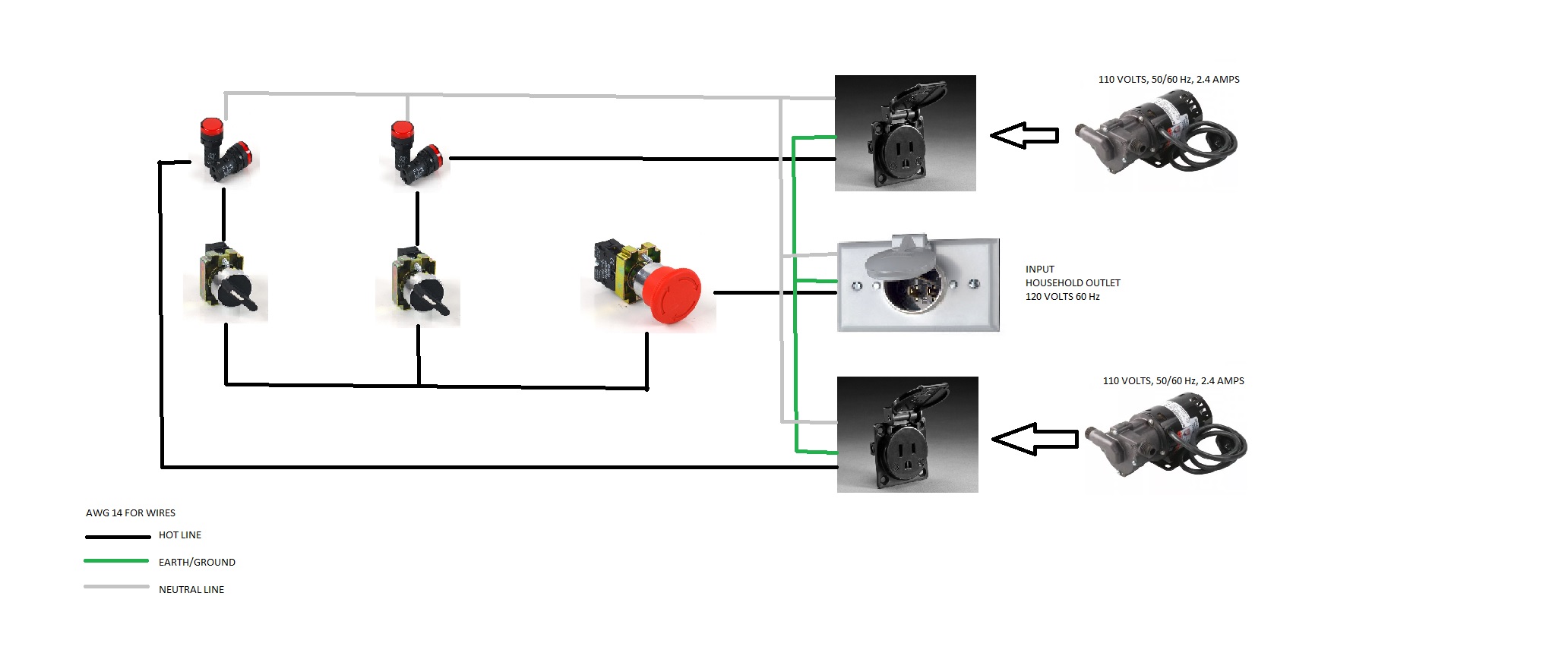
To give an idea of what I am doing with my brewing system. This will utilize 2 - 18" propane burners with two march pumps controlled by the switching module. I will also have all SS Brewing Technology (HLT/MT/BK). And a plate chiller which is not in these designs.
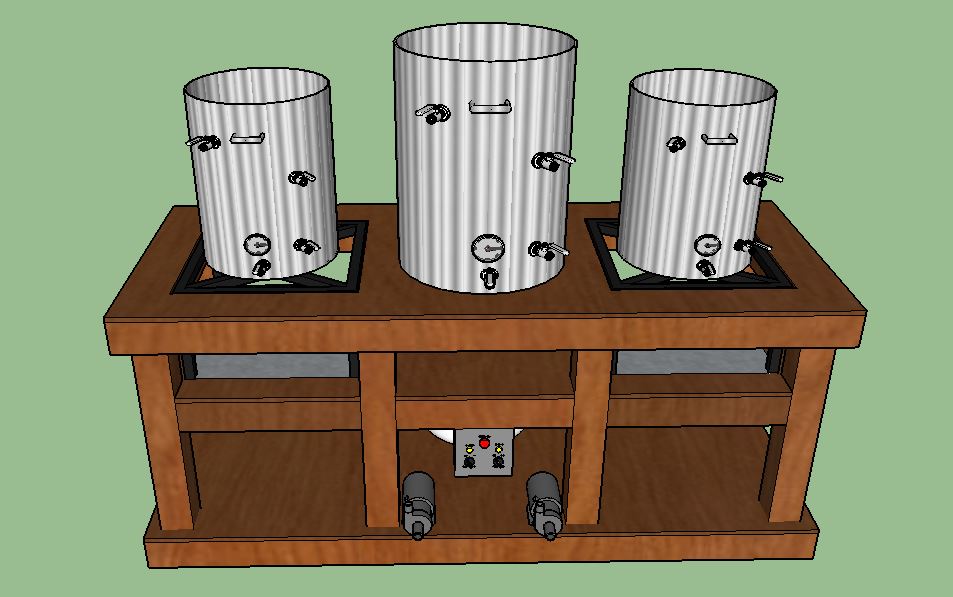
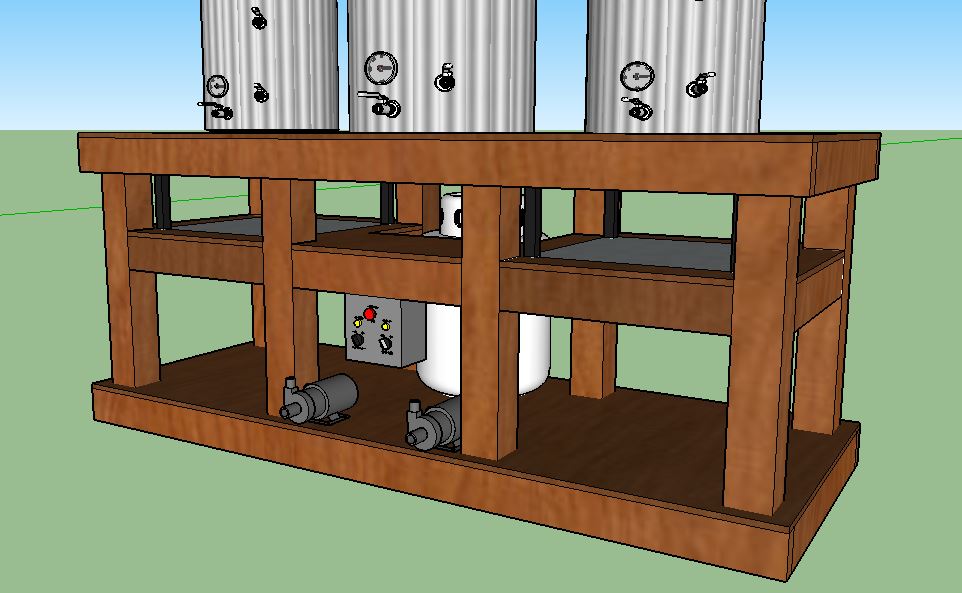
Any suggestions welcome.
Thank you!