FWIW, I kept the coil out of the HLT and just recirc the HLT as the control through the convoluted CFC and the wort in the opposite direction. When it is time to cool, I just switch the valves, and start running water through the opposite direction. Since I'm recirculating the HLT liquor I don't need the use of a motor nor a paddle to keep temperatures even. Having the connections to the faucet are also great when filling and cleaning the system. I know a lot of folks choose to pump the wort through the coil in the HLT, I just chose a different route.
A shot of the pumps and heat/cool exchanger. The hose connections are also a great way for flushing the copper coil and filling up kettles for cleaning.
Regarding the thermoplastic, it's completely opaque so there's no watching the wort through the lines. I use polysulphone QD's and have been very pleased with the design.
I'm looking fwd to seeing your system built and brewing away! If my Dad and brother were here in the NJ, I'm sure I would have two committed brew buddies.
A shot of the pumps and heat/cool exchanger. The hose connections are also a great way for flushing the copper coil and filling up kettles for cleaning.
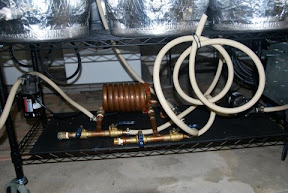
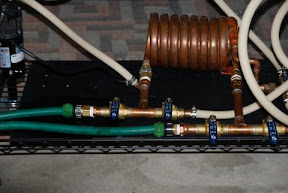
Regarding the thermoplastic, it's completely opaque so there's no watching the wort through the lines. I use polysulphone QD's and have been very pleased with the design.
I'm looking fwd to seeing your system built and brewing away! If my Dad and brother were here in the NJ, I'm sure I would have two committed brew buddies.