BradnerBrewer
New Member
First up, I ordered what was supposed to be a stainless steel bulkhead specifically for a cooler. I'm using the 10gal orange Rubbermaid "Home Depot" one. The bulkhead is described as, "fitting for most cylindrical coolers with a maximum usable clearance of about 1" (Minimum 5/8")". That's me!
I tried a couple different sized nipples. The first, as you can see, doesn't protrude into the cooler enough to attach anything to:
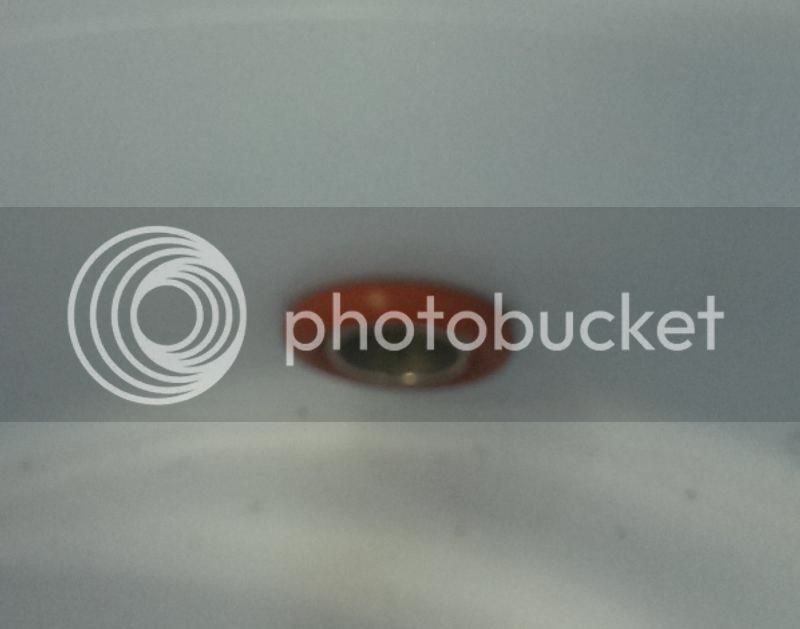
The longer one, despite using three washers as spacers, plus a large o-ring, wasn't enough to make it tight enough for a proper seal. One more washer would do it, but seriously, I have to use 4 washers to make this work? It makes no sense.
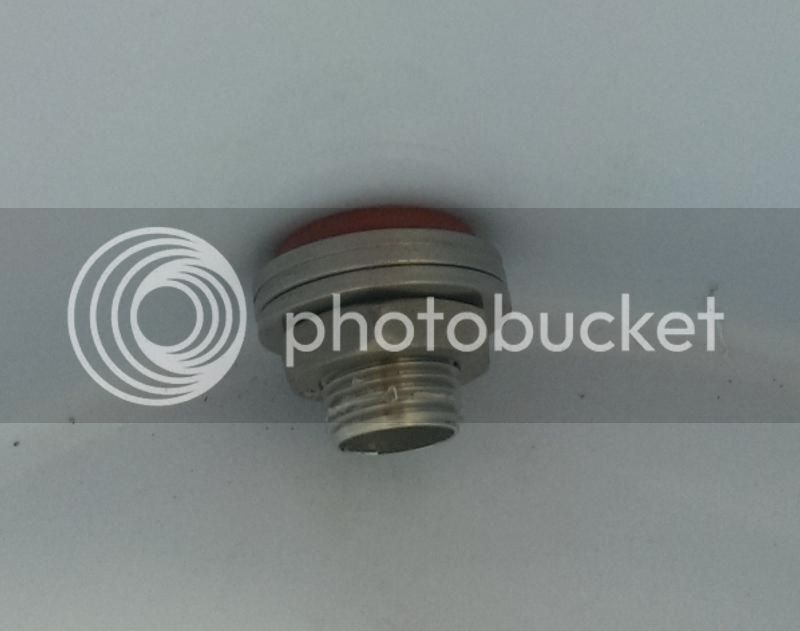
On the outside, I used a large washer and an o-ring. I used the o-ring primarily as a spacer so the valve would clear the cooler sufficiently to close it. I figure that's the only part I got right since the valve worked.

As for the keggles, I'm still having issues finding the right combination of bits and pieces to make it work, but I think I'll resolve the cooler issue first, then move on to the keggles.
As you can see, I have a good selection of parts and they were ordered specifically for their intended use; 2 stainless steel weldless bulkheads for the keggles and one for the cooler (one valve is not pictured here).
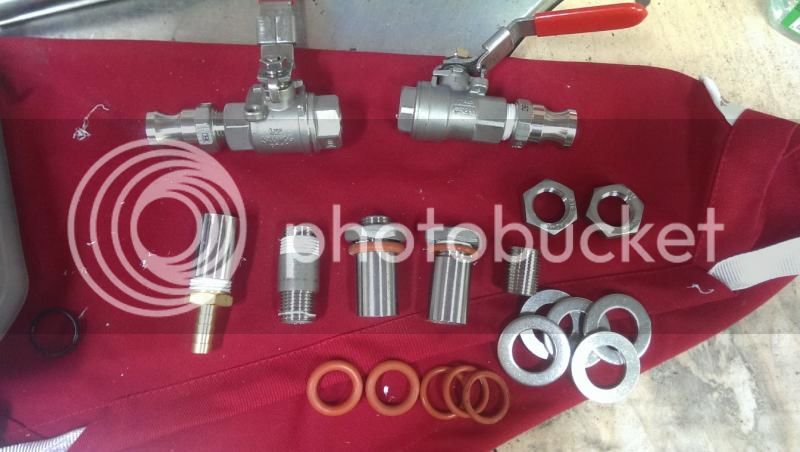
Any insight, assistance and/or guidance would be very much appreciated.
I should note that I did contact the supplier for assistance and was basically told, "how ever you can get it to work and not leak is fine". Yeah, well, thanks for that.