purplehaze
Well-Known Member
- Joined
- Mar 2, 2011
- Messages
- 398
- Reaction score
- 27
Figured I would pass on some info I came across that helped me reduce the amount of propane and time it takes to brew outside during winter. It always seemed to take forever for my wort to boil. I ended up building an insulated pot skirt out of some $12 aluminum flashing, rivets and a cheap fiberglass welding blanket. I actually got a few ideas from threads here and then stumbled upon this link below that has lots of info.
http://www.vrac.iastate.edu/ethos/f... and Heat Transfer/Skirts Paper_Andreatta.pdf
When I built and tested the skirt it was a windy 32 degree day. With 6 gallons of 130 degree wort it took 16minutes to bring it to a rolling boil. I did open the lid to take a temp reading at 10 minutes and it was already at 200 degrees. I was surprised the first time I used it when it started boiling from the sides instead of from the bottom.
Normally Exhaust gasses come out from under the keggle and dissipate on the wind. The skirt captures these gases and forces them up the sides of the keggle adding heat. Additionally since the environment is cooler than the pot, it also loses heat from the sides. Adding insulation to the skirt keeps most of the heat in the pot.
The aluminum is very flimsy and requires some rebending of the bottom to keep it symmetrical and to reduce the crumpled areas that occur between brew days. I did rivet some bent aluminum standoffs to the base of skirt in an effort to maintain an equal gap all the way around. One thing I do not like about this is that I cannot see the flames on my burner.
http://www.vrac.iastate.edu/ethos/f... and Heat Transfer/Skirts Paper_Andreatta.pdf
When I built and tested the skirt it was a windy 32 degree day. With 6 gallons of 130 degree wort it took 16minutes to bring it to a rolling boil. I did open the lid to take a temp reading at 10 minutes and it was already at 200 degrees. I was surprised the first time I used it when it started boiling from the sides instead of from the bottom.
Normally Exhaust gasses come out from under the keggle and dissipate on the wind. The skirt captures these gases and forces them up the sides of the keggle adding heat. Additionally since the environment is cooler than the pot, it also loses heat from the sides. Adding insulation to the skirt keeps most of the heat in the pot.
The aluminum is very flimsy and requires some rebending of the bottom to keep it symmetrical and to reduce the crumpled areas that occur between brew days. I did rivet some bent aluminum standoffs to the base of skirt in an effort to maintain an equal gap all the way around. One thing I do not like about this is that I cannot see the flames on my burner.
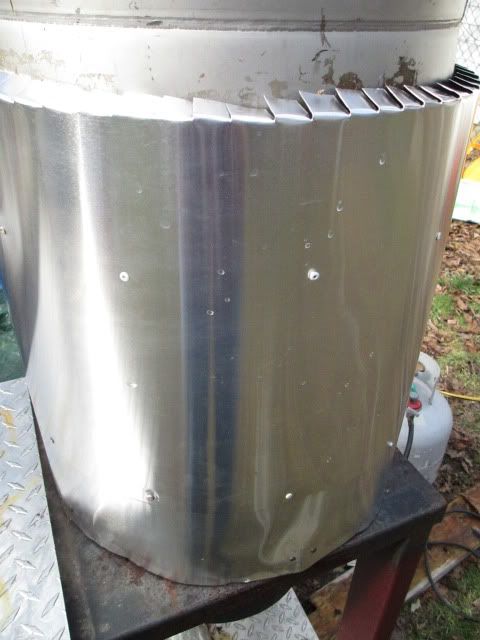
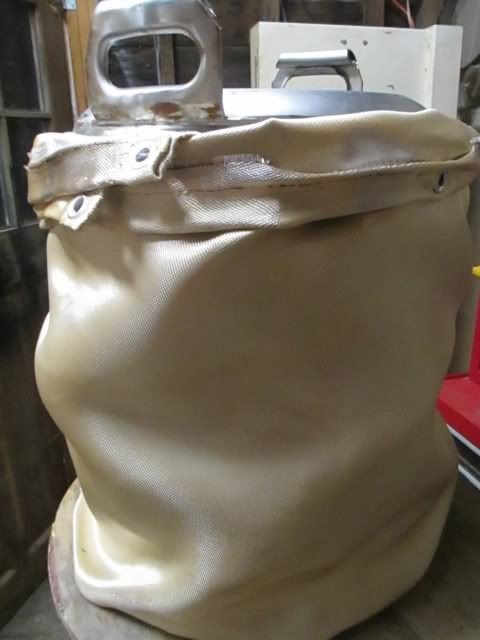