Gonefishing
Someday I'll stop procrastinating
I picked up this box today at the Goodwill store. It's a bit deep, but it's sturdy metal and at $6 I couldn't leave it sitting there.
I think I might add some sliding shelves to put the components on because the box is 13 inches deep... which is also the height and width. In its original incarnation, it was a file box.
I think I might add some sliding shelves to put the components on because the box is 13 inches deep... which is also the height and width. In its original incarnation, it was a file box.
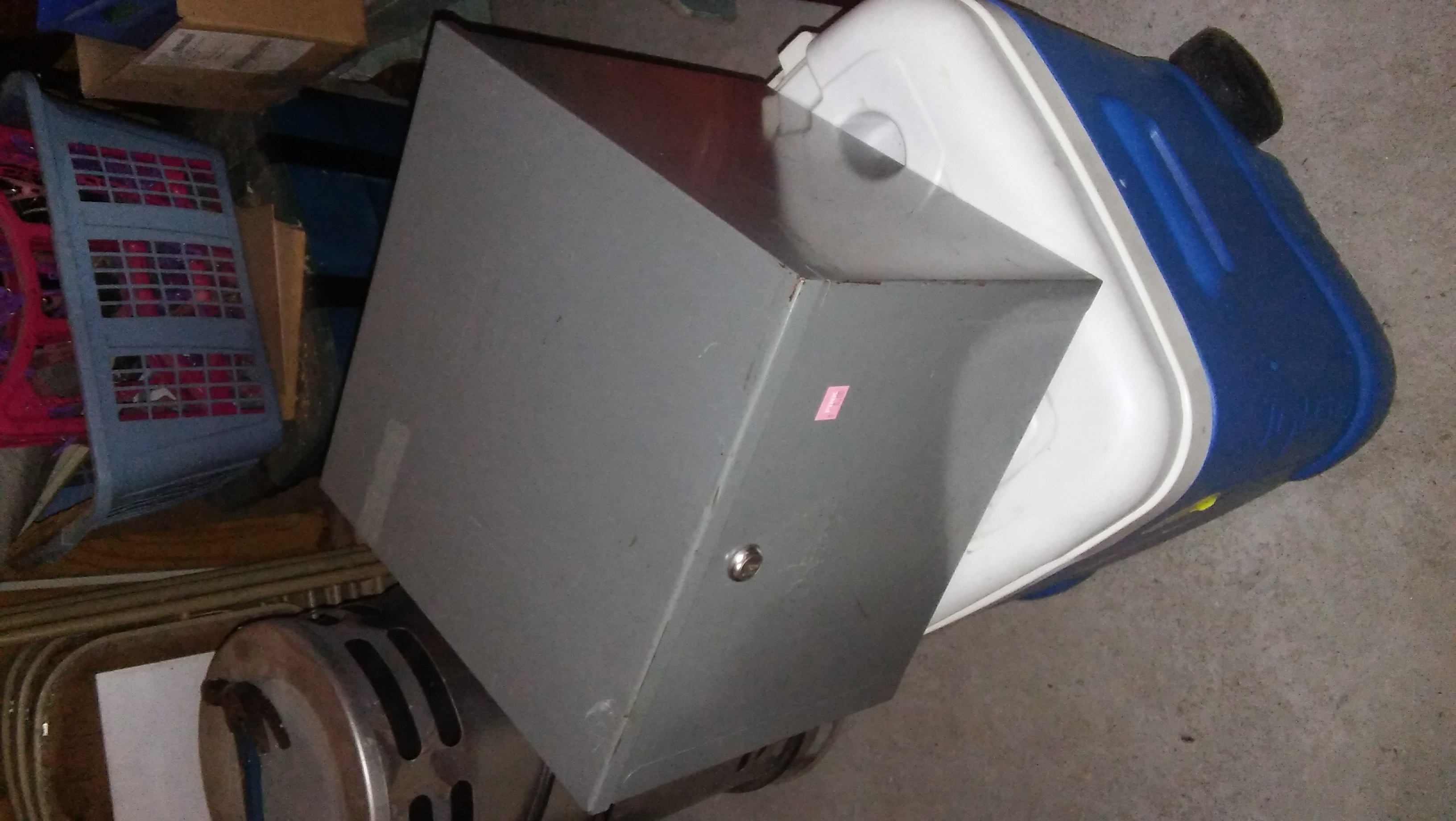