I'm building a 10"x19" hop spider to use for a few batches in my current BK which is a keggle (the one in all of the previous photos). I'm about to convert to a HERMS system, so the keggle will become a HLT. If the hop spider works well in my keggle, I'm going to build a bigger version (12"x19") for the new BK. It seems like a lot of work for one or two batches before the HERMS system is ready, but I want to prove that the design works before I build the final version for the new BK.
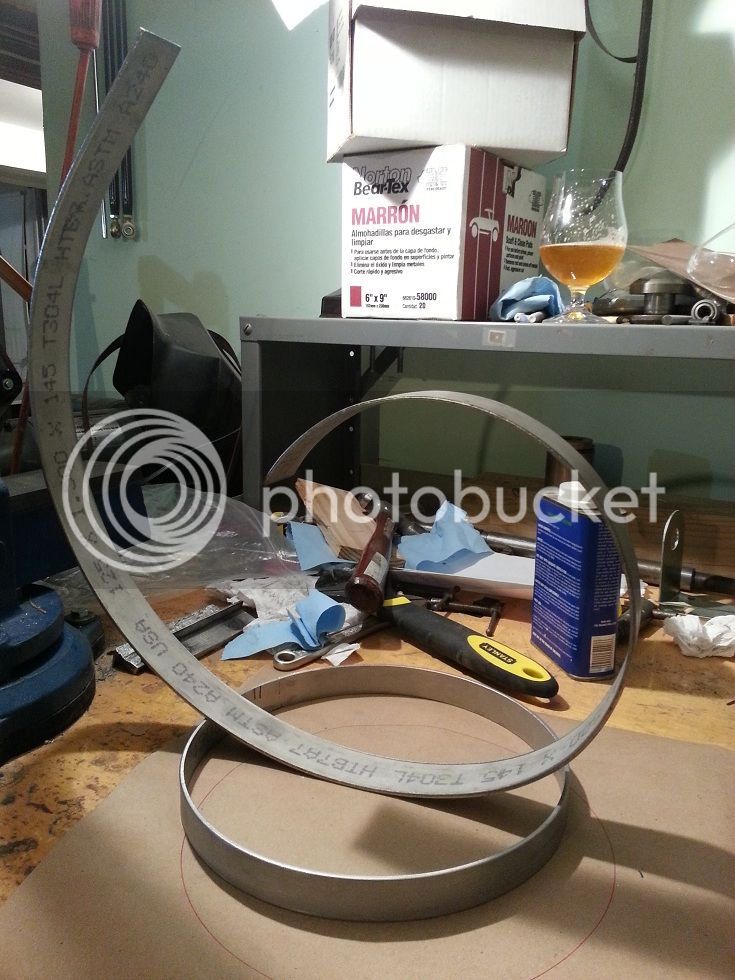
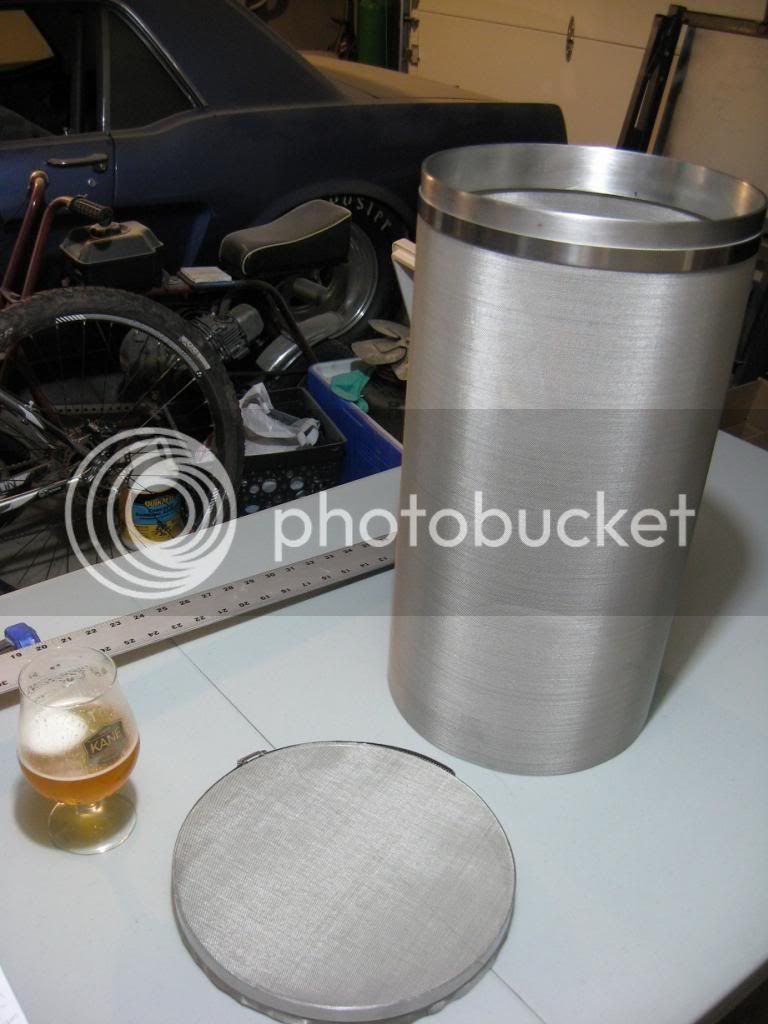