- Joined
- Nov 18, 2008
- Messages
- 2,058
- Reaction score
- 25
Wow... I'm now even more impressed by the work that some of the folks have shown here. Even IF you get everything set right (not sure I have done that yet), managing the pedal, feeding the rod, keeping the torch a consistent distance and speed is A LOT to coordinate.
After a few more practices:
After a few more practices:
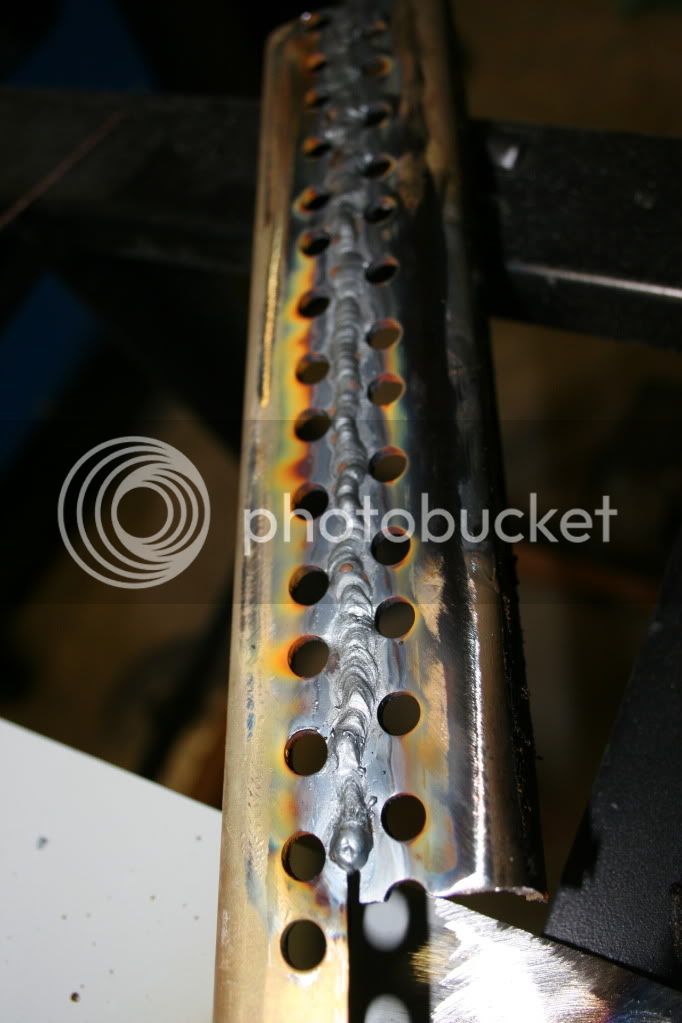