Weezy
Well-Known Member
I have a couple thermal wires, and have had for years. One is liked 932 Watts. The other is 260 Watts. When plugged into 110v, both get to the 290-320°F range. They're rated to like 1,400°F before they'd burn.
One of my induction cookers died so I pulled them back out to play with. I decided a use for both, this is the first I'll post about. The first is a RIMs tube using the 260W wire. made out of a short piece of copper, a 2" diameter piece of PVC pipe, two matching end caps, and some insulation for the wire. The insulation is ceramic blanket stuff, 1" thick, for wood stoves (rated to like 2,200°F).
Assembly was dreadfully simple. Wrap the wire tightly around the copper. Cut the PVC and insulation to be a little longer than the length of the wrapped wire. Drill holes in the end caps. Cut slots along end of tube to allow the plug wires to sneak out between the end cap and end of pipe.
The finished product that took about 20 minutes to make:
At 260W it does a surprising good job of maintaining mash temps (with the 930W one you could step mash). And at 260W (2.1 amps) you could use anything to control the temp. And the best part about thermal wires???? No wort touching the heating element and stupid easy to clean.
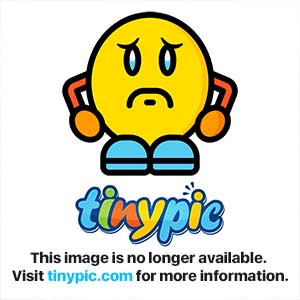
One of my induction cookers died so I pulled them back out to play with. I decided a use for both, this is the first I'll post about. The first is a RIMs tube using the 260W wire. made out of a short piece of copper, a 2" diameter piece of PVC pipe, two matching end caps, and some insulation for the wire. The insulation is ceramic blanket stuff, 1" thick, for wood stoves (rated to like 2,200°F).
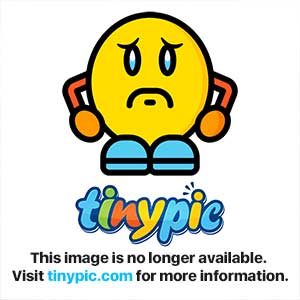
Assembly was dreadfully simple. Wrap the wire tightly around the copper. Cut the PVC and insulation to be a little longer than the length of the wrapped wire. Drill holes in the end caps. Cut slots along end of tube to allow the plug wires to sneak out between the end cap and end of pipe.
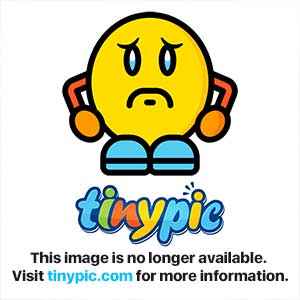
The finished product that took about 20 minutes to make:
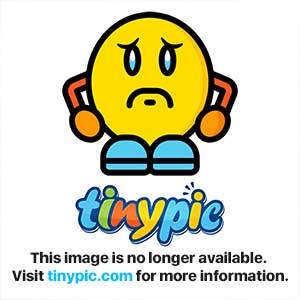
At 260W it does a surprising good job of maintaining mash temps (with the 930W one you could step mash). And at 260W (2.1 amps) you could use anything to control the temp. And the best part about thermal wires???? No wort touching the heating element and stupid easy to clean.