Today was to be the first AG in my "long time coming" all electric HERMS rig in the basement. I'm running it through a 2 pole 30amp 10ka 240 feed backed with a Square D 30amp GFCI panel breaker. The feed goes straight into my control panel and runs all my electrical needs. Here's a picture of my rig and more importanly a pic of the control box.
The 2 pole switch on the lower left handles one hot leg of the 240 and splits it between my two electrical heater elements . The SSR and PID/temp controllers handle the other leg of the hot so I can completely disable any electricity to the heating elements(it's 20amp switch but I'm wondering if I really need this). The yellow plugs go to 2 march pumps. The pumps and PID's are all fused and all grounds including grounds on keggles terminate back to the panel through the electrical feed.
When I'm running my rig during the Mashing process I will have one Auber PID(nominal) two March pumps (1.4a) running and one 3500w 240v heater element. During the boil I have only one PID and one 3500w element running. My math says even under full load I should be drawing no more than 21-23amps.
So today after running the system for a couple hours(cleaning, sanitizing, Auto tuning, and then beginning my brew process, my GFI panel breaker tripped. I turned off all of the pumps, PIDS, neutralized the elements, and while my lead was still plugged into the outlet, it would not reset. I unplugged it from the wall, reset the breaker and it stayed. I plugged my plug back into the wall and it tripped. I felt for any heat and didn't feel any at all on my control panel or any of the cables. Once I did manage to get the breaker set and plugged back in, i turned on the two march pumps and the PID sans elements and it tripped again.
Now I've accepted defeat for today and I'm hoping that the many talented folks whom I've learned everything from may have some insight into how I may troubleshoot this out.
I want to get my first AG started so I can start to back up my ridiculous investment of time, money, and effort with a delicious beer.
On a lighter note, I'm starting my daughter young on identifying the various hops and their aromas
Flananuts
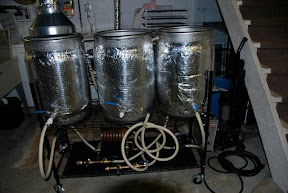
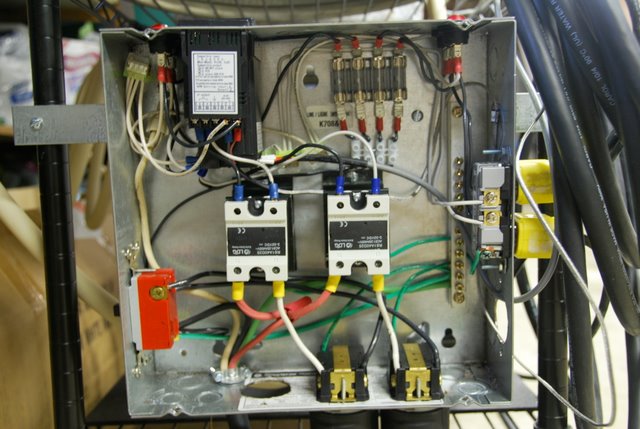
The 2 pole switch on the lower left handles one hot leg of the 240 and splits it between my two electrical heater elements . The SSR and PID/temp controllers handle the other leg of the hot so I can completely disable any electricity to the heating elements(it's 20amp switch but I'm wondering if I really need this). The yellow plugs go to 2 march pumps. The pumps and PID's are all fused and all grounds including grounds on keggles terminate back to the panel through the electrical feed.
When I'm running my rig during the Mashing process I will have one Auber PID(nominal) two March pumps (1.4a) running and one 3500w 240v heater element. During the boil I have only one PID and one 3500w element running. My math says even under full load I should be drawing no more than 21-23amps.
So today after running the system for a couple hours(cleaning, sanitizing, Auto tuning, and then beginning my brew process, my GFI panel breaker tripped. I turned off all of the pumps, PIDS, neutralized the elements, and while my lead was still plugged into the outlet, it would not reset. I unplugged it from the wall, reset the breaker and it stayed. I plugged my plug back into the wall and it tripped. I felt for any heat and didn't feel any at all on my control panel or any of the cables. Once I did manage to get the breaker set and plugged back in, i turned on the two march pumps and the PID sans elements and it tripped again.
Now I've accepted defeat for today and I'm hoping that the many talented folks whom I've learned everything from may have some insight into how I may troubleshoot this out.
I want to get my first AG started so I can start to back up my ridiculous investment of time, money, and effort with a delicious beer.
On a lighter note, I'm starting my daughter young on identifying the various hops and their aromas
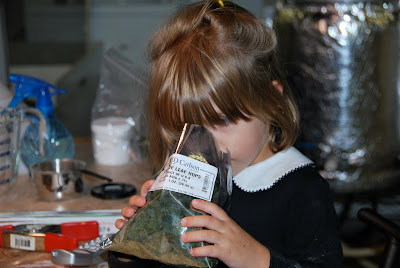
Flananuts