99blackgt
Well-Known Member
Ok, so we have a few kegs left over from partying back in the day. Figured we'd get some good use out of them. I had a rubber one that i thought would be completely worthless. But i found a use for it.
Cut the normal hole in the top, put a spigot in it, and went to town.
This is her in all her beauty
From there, i used a compression fitting, to connect my initial run of 3/8ths copper tubing. Soldered the fitting because i didn't trust it, and i didn't want to have to crank on the fitting every time. The point of using a compression fitting here, was so that i could put this nut on hand tight, and the element could rotate freely from the nut untill you get it pretty tight, so i didn't have to spin it around while trying to fasten the nut. This makes removal and cleanup 100x easier.
Next i took the rest of the copper, and decided to make a double ring element. I thought about doing the same as above with compression fittings, but at $7 a fitting, there was no chance. Instead I found 1/8th" copper FIP fittings (at a much better $1.25 a piece). These are solid, but meant for very small threaded tubes. Advantage of this was, the ID of these fittings was almost identical to the OD of my tubing. Because this copper has much thinner walls than the tube designed to go with these fittings. Obiviously though, i can't just thread standard tubing into these fittings; so i decided to solder them.
Cut the normal hole in the top, put a spigot in it, and went to town.
This is her in all her beauty
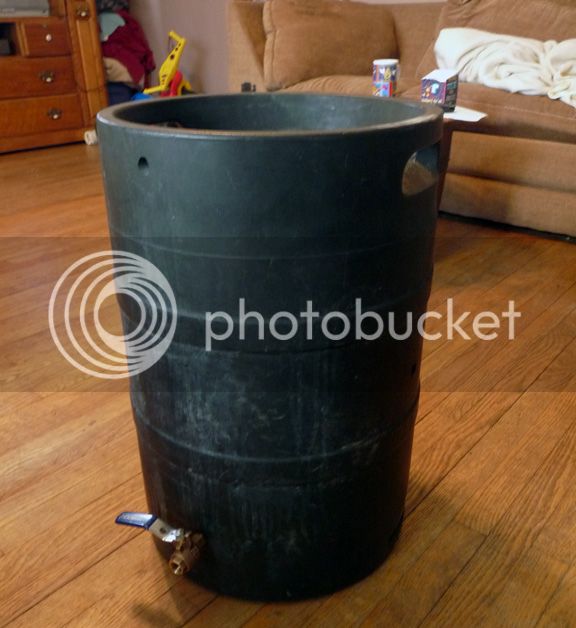
From there, i used a compression fitting, to connect my initial run of 3/8ths copper tubing. Soldered the fitting because i didn't trust it, and i didn't want to have to crank on the fitting every time. The point of using a compression fitting here, was so that i could put this nut on hand tight, and the element could rotate freely from the nut untill you get it pretty tight, so i didn't have to spin it around while trying to fasten the nut. This makes removal and cleanup 100x easier.
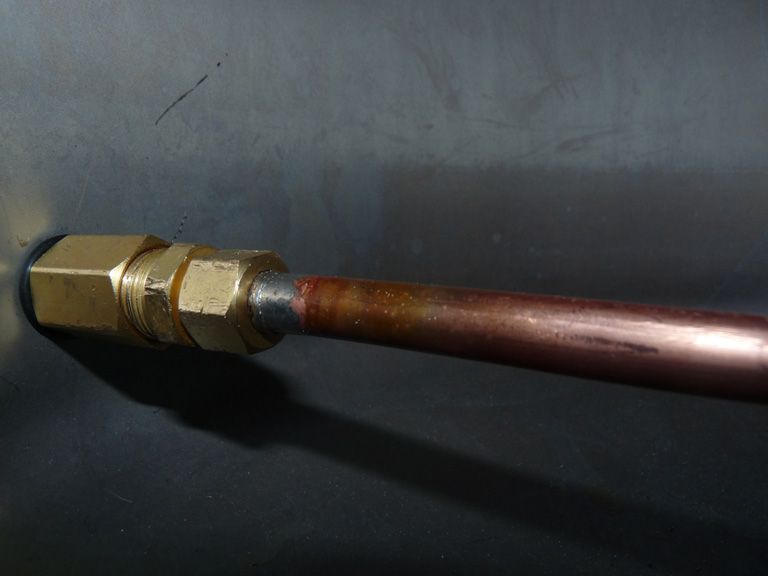
Next i took the rest of the copper, and decided to make a double ring element. I thought about doing the same as above with compression fittings, but at $7 a fitting, there was no chance. Instead I found 1/8th" copper FIP fittings (at a much better $1.25 a piece). These are solid, but meant for very small threaded tubes. Advantage of this was, the ID of these fittings was almost identical to the OD of my tubing. Because this copper has much thinner walls than the tube designed to go with these fittings. Obiviously though, i can't just thread standard tubing into these fittings; so i decided to solder them.
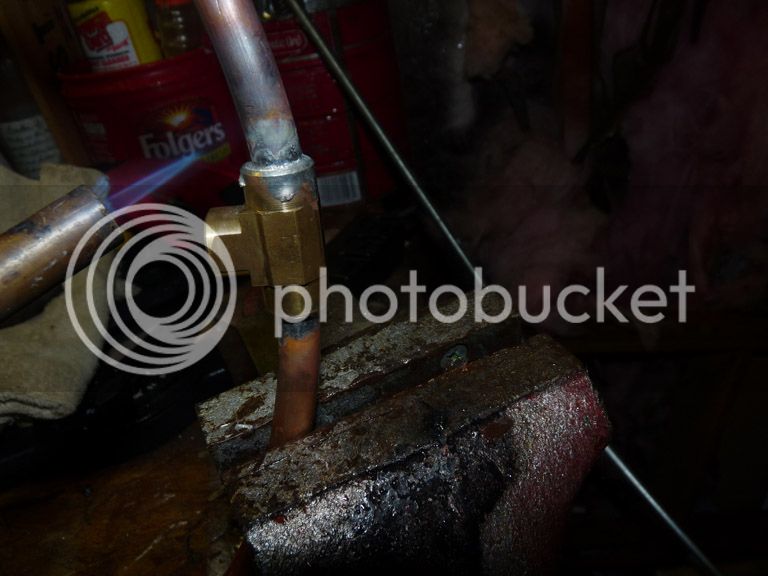
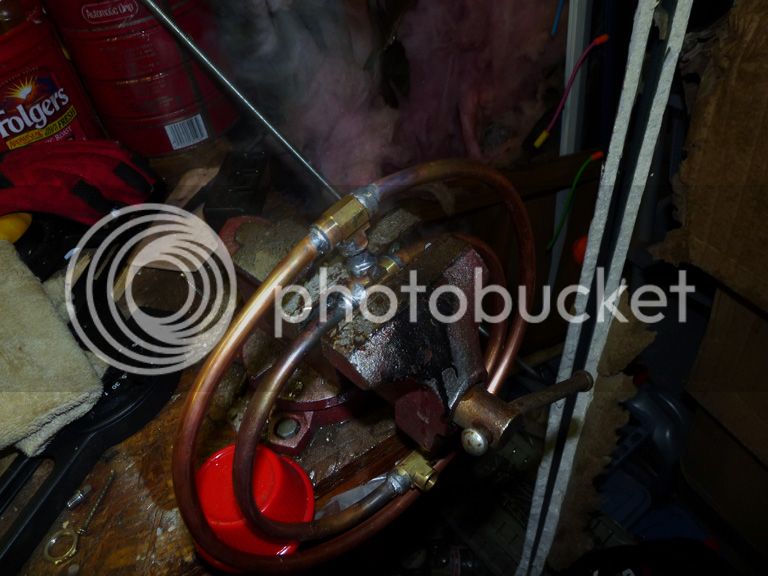