mullet
Well-Known Member
After hand-cranking all of my grain for over a year, I've finally decided to take the plunge and motorize my grain mill.
First off, I needed a stand. I've been down the road of building things before, and it never turns out as cheap as I'd like, so I started poking around classifieds ads to see if I could find a suitable stand, cupboard, vanity, etc... Picked this one up for $25.
The door part would be great to keep dust down a bit and there is an identical door on the other side. The unfortunate part is the drawer at the top. It just slides in there, and it pulls out to either side. I'd like to mount the mill and motor under the table, with inspiration from this setup. So that drawer had to go. I took the top off the cabinet (was held on with 4 allen key bolts) I took the drawer out, disassembled it, and added some hinges to the faces of the drawer, and attached them back to the cart. This should allow me to get at the gap adjusting parts after I put it all together.
Next I needed a motor. I have an MM2, which only has 2 1.5" rollers, so I figured the standard recommended motor would probably have enough torque for me, and I ordered one up. For any other Canadians, shipping to Canada was ~$40 by USPS priority mail and the motor showed up in 6 days. (4 business days)
Here is where I have a question. The motor is sliiightly larger in diameter than the height of the space between the shelf and the bottom of the cart surface. But, if I take off the fan cover and fan, as shown below, I think I can elevate the top using some washers enough to squeeze the motor in there.
My question is, is it ok to take off the fan, or is that not really recommended? I figure if I was planning to actually run the motor continuously, that it would probably be an issue. But for the 4 or 5 minutes that I'd be milling grain, it probably isn't a big deal. Anyone got an opinion on that?
I also ordered the parts I'd need for the direct drive coupler from McMaster. Found out the next day that McMaster doesn't ship to Canada. Fair enough. Tried my local Princess Auto, found they had lots of sheaves, belts, sprockets, and chain, but no couplers. So after looking around online, I discovered that there was a Fastenal just around the corner from work and they can order the parts I need. It was a few dollars more expensive than McMaster, (I think the total for McMaster before shipping was ~$10, while the Fastenal order was something like ~$17) but there was no shipping, so I figure it's probably about the same. Here are the part numbers for anyone in Canada who might be curious:
3/8" Hub (For Mill) - Fastenal: 0439466 - McMaster: 6408K123
1/2" Hub (For Motor) - Fastenal: 0439470 - McMaster: 6408K712
Spider Insert - Fastenal: 0439459 - McMaster: 6408K73
I'll post up an electical drawing next.
First off, I needed a stand. I've been down the road of building things before, and it never turns out as cheap as I'd like, so I started poking around classifieds ads to see if I could find a suitable stand, cupboard, vanity, etc... Picked this one up for $25.

The door part would be great to keep dust down a bit and there is an identical door on the other side. The unfortunate part is the drawer at the top. It just slides in there, and it pulls out to either side. I'd like to mount the mill and motor under the table, with inspiration from this setup. So that drawer had to go. I took the top off the cabinet (was held on with 4 allen key bolts) I took the drawer out, disassembled it, and added some hinges to the faces of the drawer, and attached them back to the cart. This should allow me to get at the gap adjusting parts after I put it all together.
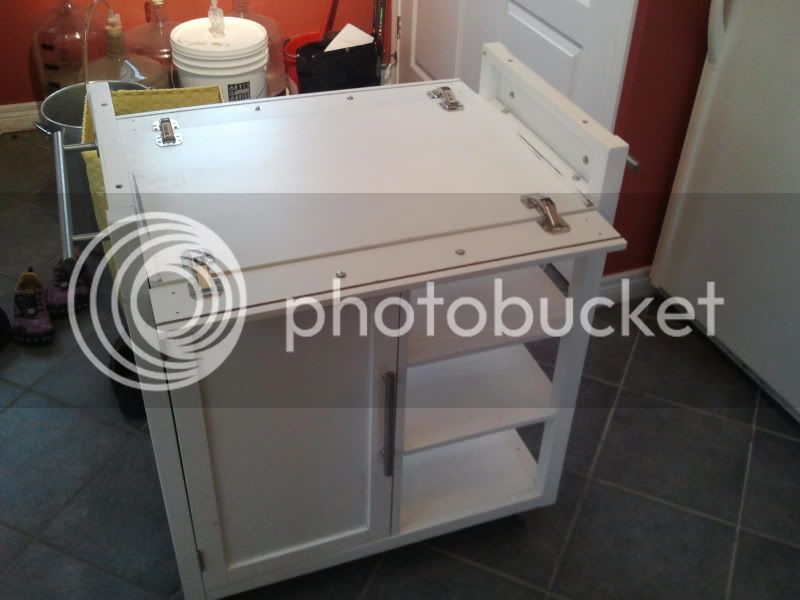
Next I needed a motor. I have an MM2, which only has 2 1.5" rollers, so I figured the standard recommended motor would probably have enough torque for me, and I ordered one up. For any other Canadians, shipping to Canada was ~$40 by USPS priority mail and the motor showed up in 6 days. (4 business days)
Here is where I have a question. The motor is sliiightly larger in diameter than the height of the space between the shelf and the bottom of the cart surface. But, if I take off the fan cover and fan, as shown below, I think I can elevate the top using some washers enough to squeeze the motor in there.
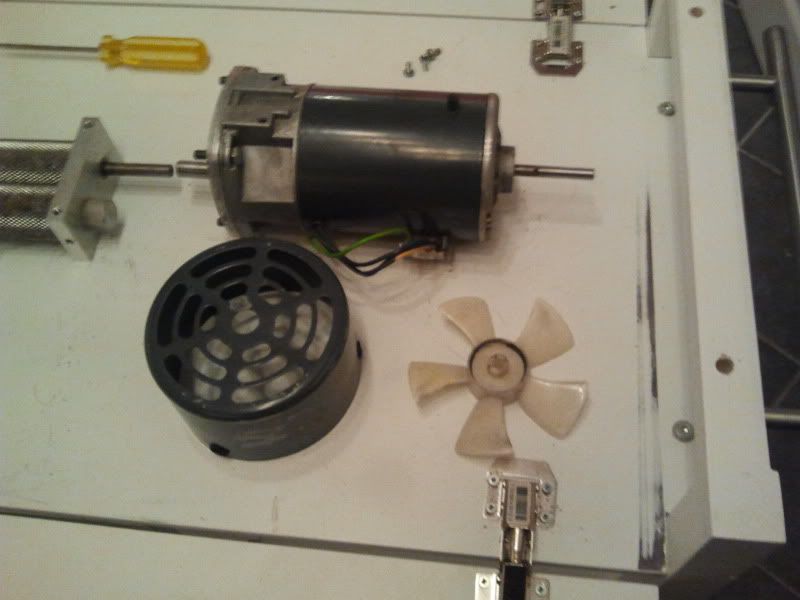
My question is, is it ok to take off the fan, or is that not really recommended? I figure if I was planning to actually run the motor continuously, that it would probably be an issue. But for the 4 or 5 minutes that I'd be milling grain, it probably isn't a big deal. Anyone got an opinion on that?
I also ordered the parts I'd need for the direct drive coupler from McMaster. Found out the next day that McMaster doesn't ship to Canada. Fair enough. Tried my local Princess Auto, found they had lots of sheaves, belts, sprockets, and chain, but no couplers. So after looking around online, I discovered that there was a Fastenal just around the corner from work and they can order the parts I need. It was a few dollars more expensive than McMaster, (I think the total for McMaster before shipping was ~$10, while the Fastenal order was something like ~$17) but there was no shipping, so I figure it's probably about the same. Here are the part numbers for anyone in Canada who might be curious:
3/8" Hub (For Mill) - Fastenal: 0439466 - McMaster: 6408K123
1/2" Hub (For Motor) - Fastenal: 0439470 - McMaster: 6408K712
Spider Insert - Fastenal: 0439459 - McMaster: 6408K73
I'll post up an electical drawing next.