First off, I must thank the folks on this site for all the great info. Without them, I don't know if I would have even attempted something like this.
Direct links to posts...
To start, I've been kegging for a short while and had a typical freezer top fridge in the basement. This is great and the finger tap got the job done, but who doesn't want their beer more readily available? Our kitchen has a butlers pantry which would be a great spot for a tap. After wife approval, we were a go.
My entire basis for the trunk line was from the following post https://www.homebrewtalk.com/f35/long-draw-salt-water-chilled-beer-tower-271578/ so a huge thanks to runningweird. My parts list:
I would highly recommend trying to straighten the tubing before you start as much as possible.
Cable tying was a pita as I only did this so much. You definitely don't want to end up with the serpentine I did!
When cable tying, you want to make sure you wrap the 4 beer lines around the out coolant line (cold) and the in coolant line (warm) next to the out.
Once you've organized the tubing in such a way, wrap a cable tie around it, move 1 ft down and do it again. Once you are all tied up, cut all the ends, wrap the saran wrap around the entire length as a moisture barrier, then tin foil as a temperature barrier, then pipe tubing and lastly electrical tape. The pipe tubing adhesive was only so good which was I used electrical tape; this is optional.
Cooling up next...
Direct links to posts...
- Trunk line - this post
- Beer line length formula and beer line cooling
- Beer tower
To start, I've been kegging for a short while and had a typical freezer top fridge in the basement. This is great and the finger tap got the job done, but who doesn't want their beer more readily available? Our kitchen has a butlers pantry which would be a great spot for a tap. After wife approval, we were a go.
My entire basis for the trunk line was from the following post https://www.homebrewtalk.com/f35/long-draw-salt-water-chilled-beer-tower-271578/ so a huge thanks to runningweird. My parts list:
- 100 ft. 1/4" ID Barrier tubing for beer - http://www.chicompany.net/index.php?main_page=product_info&products_id=2372
- Tubing for glycol - Watts 1/2 in. OD x 3/8 in. ID x 25 ft. Polyethylene Tubing from Home Depot, http://www.homedepot.com/p/Watts-1-2-in-OD-x-3-8-in-ID-x-25-ft-Polyethylene-Tubing-SPIG25/100186093#.UlSA6lBvNpV
- Cable ties - http://www.harborfreight.com/household/cable-ties/100-piece-11-black-cable-ties-60277.html
- Saran wrap - I'm guessing any will do, but my dad gave me a commercial roll of plastic wrap he had lying around which was 2 ft in width
- Aluminum foil - heavy duty Reynolds foil
- Pipe insulation - like http://www.homedepot.com/p/Armacell...T07812/100585113?N=buy9Z40kZ12kx#.UlQ7flBvNpU, but 1 1/8" instead of 3/4"
- Electrical tape
I would highly recommend trying to straighten the tubing before you start as much as possible.

Cable tying was a pita as I only did this so much. You definitely don't want to end up with the serpentine I did!

When cable tying, you want to make sure you wrap the 4 beer lines around the out coolant line (cold) and the in coolant line (warm) next to the out.
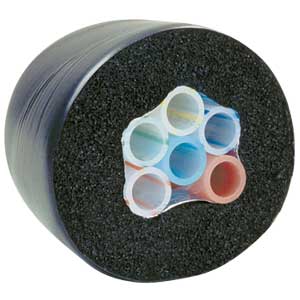
Once you've organized the tubing in such a way, wrap a cable tie around it, move 1 ft down and do it again. Once you are all tied up, cut all the ends, wrap the saran wrap around the entire length as a moisture barrier, then tin foil as a temperature barrier, then pipe tubing and lastly electrical tape. The pipe tubing adhesive was only so good which was I used electrical tape; this is optional.


Cooling up next...